Cube Compact - The Universal 360 Photography Robot
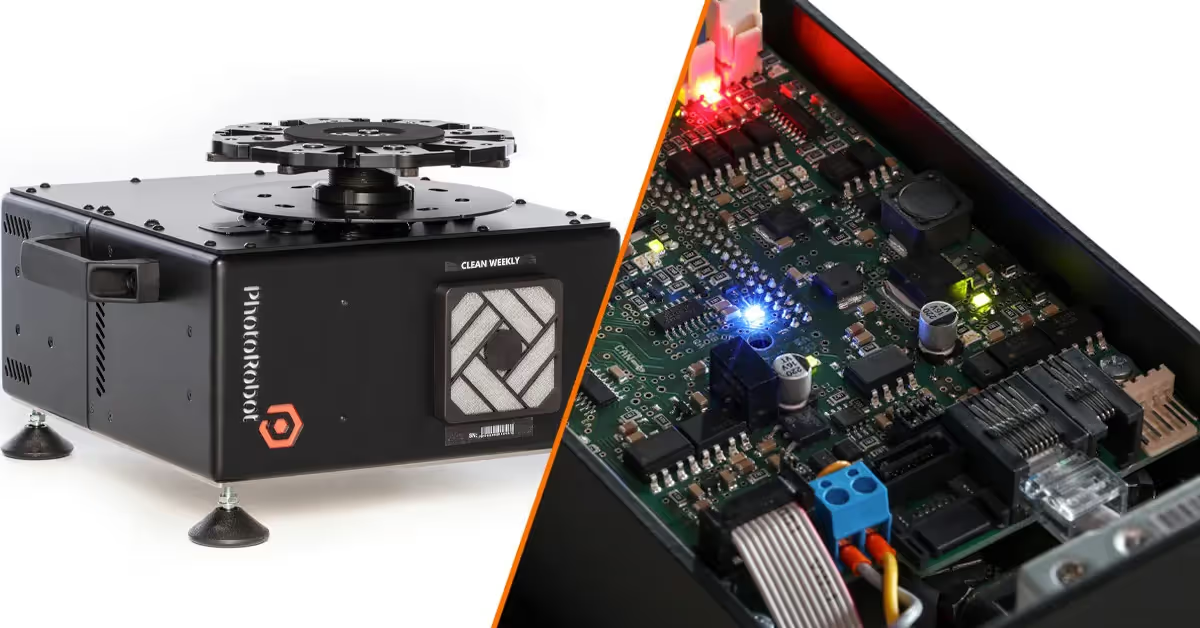
Discover the expanded functionality and features of PhotoRobot’s Cube Compact, the universal 360 product photography robot.
The Universal 360 Robot Gets an Upgrade - Cube Compact
Cube Compact is a variant of the Cube v6, the universal 360 product photography robot. These multi-purpose devices transform into standalone turntables, rotating mannequin mounts, or to suspend items in air using suspension mode. The robot is thus suitable for an extremely wide range of small to medium size products, and many photography applications.
Take for example 360 product photography of items which either cannot stand on their own or need additional support. Think of products such as handbags, bicycles, chandeliers, or light fittings. In suspension mode, the Cube can suspend items such as these above a workstation and rotate them 360 degrees.
This is in full synchronization with cameras, strobes, and lighting to automate the capture of any and all angles. The device can mount to the floor or ceiling, combine with many photographic accessories, and is compatible with other photography robots. But what makes the Cube Compact different from other versions?
Read ahead for a behind-the-scenes look at the new design and higher throughput of our universal 360 product photography robot.
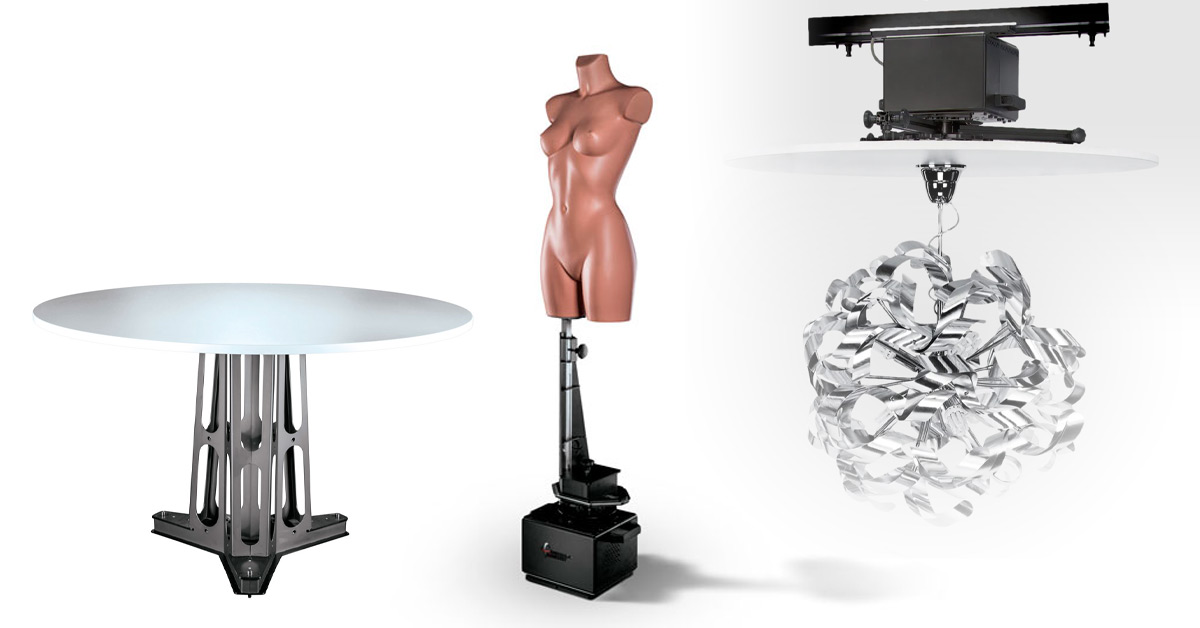
Optimized design for maximum performance
Other versions of the Cube robot feature many cooling slots on the body of the device. However, these slots can accumulate a lot of dust, especially when photographing textiles on a photography mannequin. These slots are much like the filter of a washing machine. They require regular attention and cleaning for smooth machine operation.
Now, the Cube Compact no longer features these slots. Instead, the device’s body is mostly sealed-off to eliminate the dust inlets into the machine. The airflow inside is completely controlled, while the only input is a single fan with a dust filter. At the end of the airway, a single outlet allows air to flow out of the robot.
Thus, all air flowing into the system is filtered, and there is no other way for dust to get inside. This helps when photographing large amounts of textiles, or working in a natural warehouse environment. The filter is also extremely easy to clean to ensure minimal interruption in production workflows.
At the same time, it is possible to equip the robot with a built-in laser positioning controller. This enables machine operators to connect and power the line-laser head directly with the robot. In this way, there is less cabling to worry about and no need for an additional laserbox.
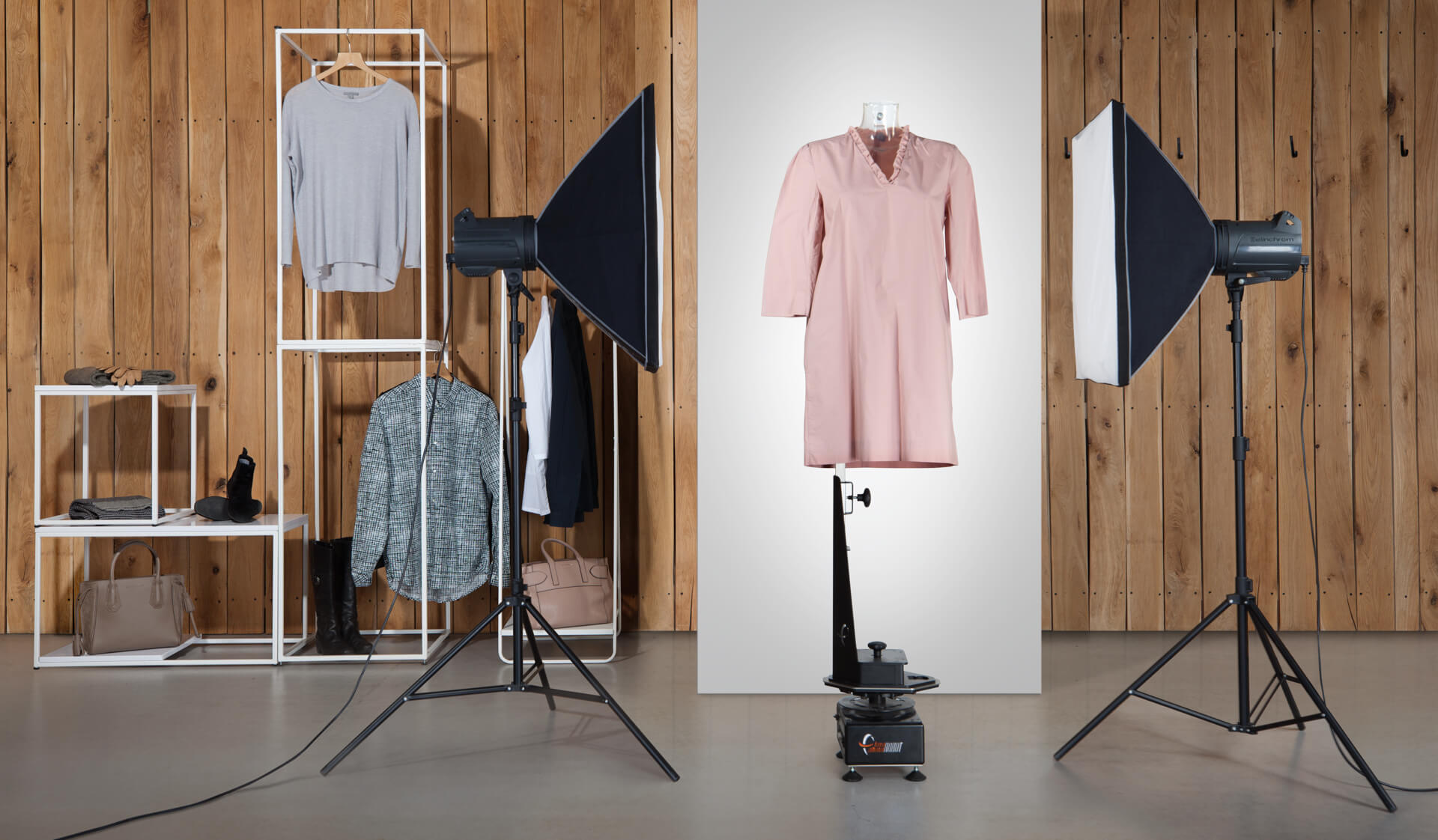
More productive photography of clothing and textiles
The Cube Compact evolved from the need to improve the device’s functionality when photographing large amounts of clothing and textiles. Surprisingly, even in climate-controlled spaces, items like these tended to accumulate and produce a lot of dust. This was an issue especially when mounting a mannequin torso to the Cube.
Thus, the design of Cube Compact aims to combat exposure to dust when working with mannequins, and prevent textile fibers from getting into the machine. And this isn’t only for photographing a few items per session. Cube Compact will support the photography of upwards of 500 objects per workspace, per shift. Meanwhile, the devices monitor thermal characteristics, and are extremely easy to clean before, after, and in-between photo sessions.
This ensures less interruption and maximum productivity in production workflows. At the same time, the hidden control unit and built-in laser output reduce potential points of failure around the workstation. There is no cabling to stumble over, and there is no longer a need for an additional laserbox. These both reduce the amount of machinery necessary for production, and mean more space for photographers to move around freely.
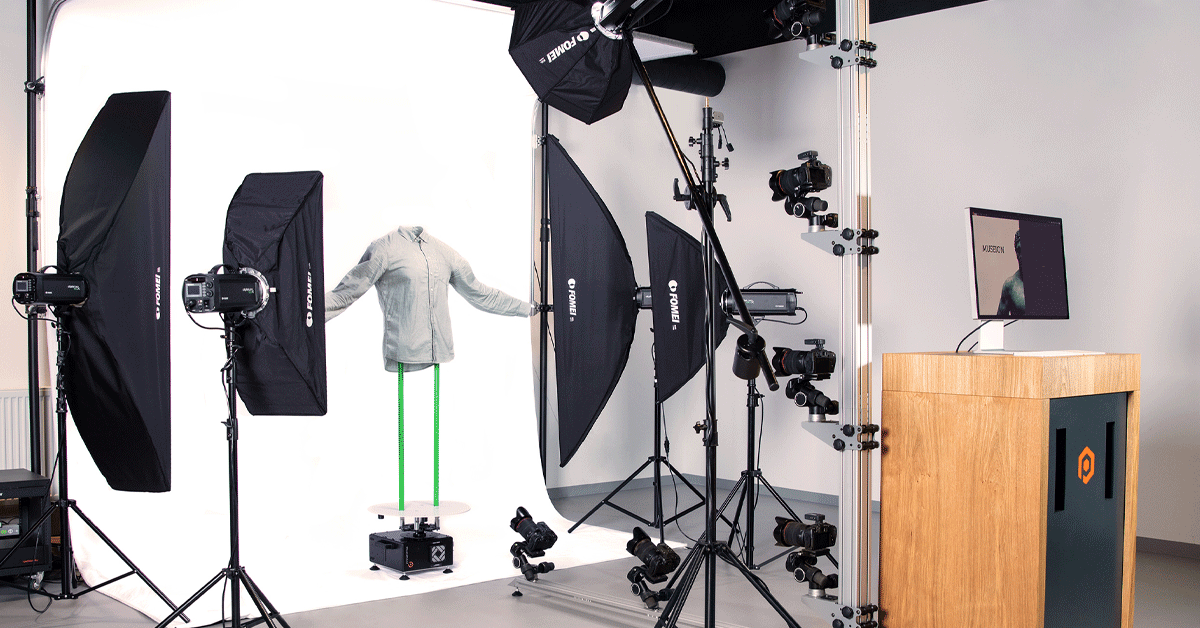
Same reliable hardware and photographic accessories
Really, it’s the same power clients expect of PhotoRobot’s Cube, just more compact in design. The Cube Compact features the same high-quality machining and 130 kg load-bearing capacity as all Cube devices. This is in all modes of operation: using the standalone 100 cm-diameter turntable, the mounting system, or in suspension mode. Meanwhile, zero-clearance transmission provides surgical precision even at maximum loads.
Automated control software then syncs the Cube to other devices, cameras, lights, and robots for complete studio control. Further, a quick-mounting system supports the Cube’s easy installation onto various workstations. This makes it easy to set up the device on its own, or in combination with other robots in a matter of minutes.
Additionally, it’s possible to compliment the Cube’s quick mannequin exchange system with an optional mannequin storage cart. The cart can transport up to six mannequins of different sizes and shapes from one station to the next. Team members can then prep mannequins in advance and off to the side. They are then easy to mount onto the Cube when ready. There is also more space to wheel carts around thanks to the device’s hidden cabling.
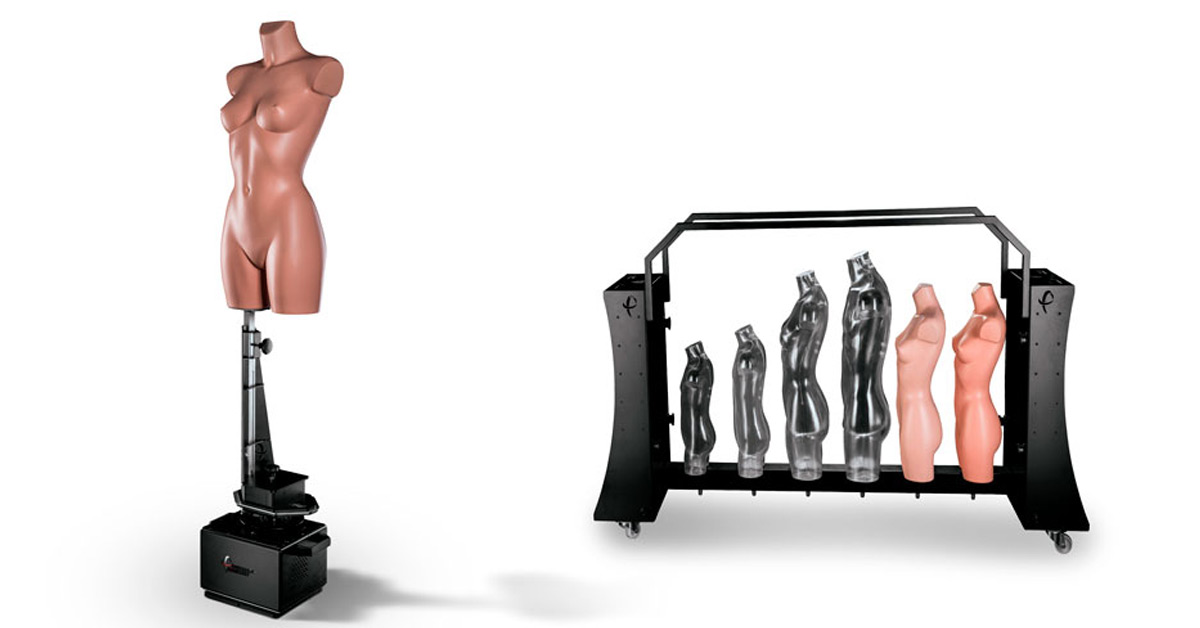
Rapid development per business’ needs
Cube Compact is available for rapid development as per business’ requirements (even unspoken). This includes for small to medium size, or industrial-scale operations. Really, it makes no difference if ordering one or 100+ robots.
As the manufacturer, PhotoRobot provides clients direct access to the factory and software development for extremely short innovation cycles. In this way, it’s possible to rapidly develop industry-specific solutions tailor-made to any business, and at a very reasonable price.
Together with customers, PhotoRobot technicians account for the quantity of items to photograph, types of products, and their weights & dimensions. It is then possible to suggest a workstation of one or multiple robots around the client’s available space and requirements.
Sometimes, it’s updating an existing area, while for others, it is building a completely new studio from the ground-up. Direct communication with hardware and software development ensures smooth onboarding of the technology, as well as optimal functionality. This is in addition to access to the latest tools and features.
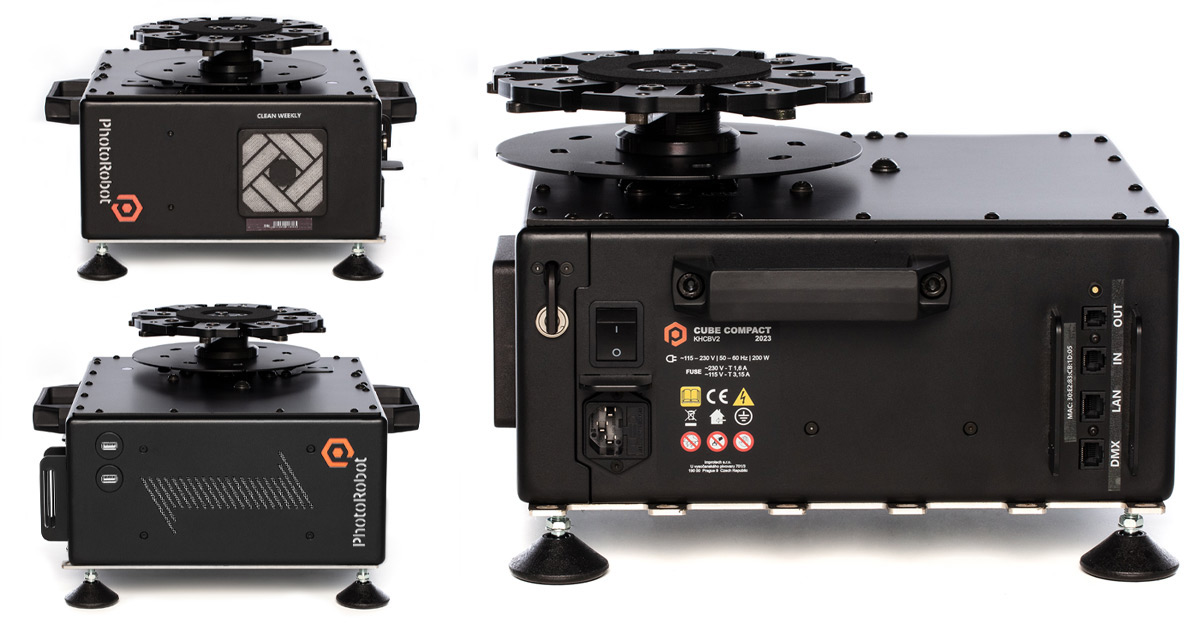
Smart software and convenient presets
No technical knowledge, no problem. PhotoRobot’s smart software works across all hardware and makes it easy to connect, synchronize, and control multiple photography robots. It commands all devices (robots, cameras, lights), and enables remote studio control as well as pre-programmable automation.
The software integrates workflow, post-processing, and digital asset management to simplify, speed up, and standardize every stage of production. Meanwhile, its unique, built-in industrial operating system runs on MacOS or Windows, supports API connection, and receives remote software updates.
Customizable user interface options then make the controls adaptable to various operator levels, and provide a range of smart functions. These include convenient presets for different types of products or outputs, as well as basic to advanced post-processing operations. In this way, anyone can take photos adhering to a style guide or image requirements within seconds.
Automation takes on repeatable processes like background removal or image adjustments and enhancements. It can even automatically create spin images, or generate 3D models from photographs. This is often with web-ready results that require minimal to no retouch, from complete galleries of packshots to 360 spins.
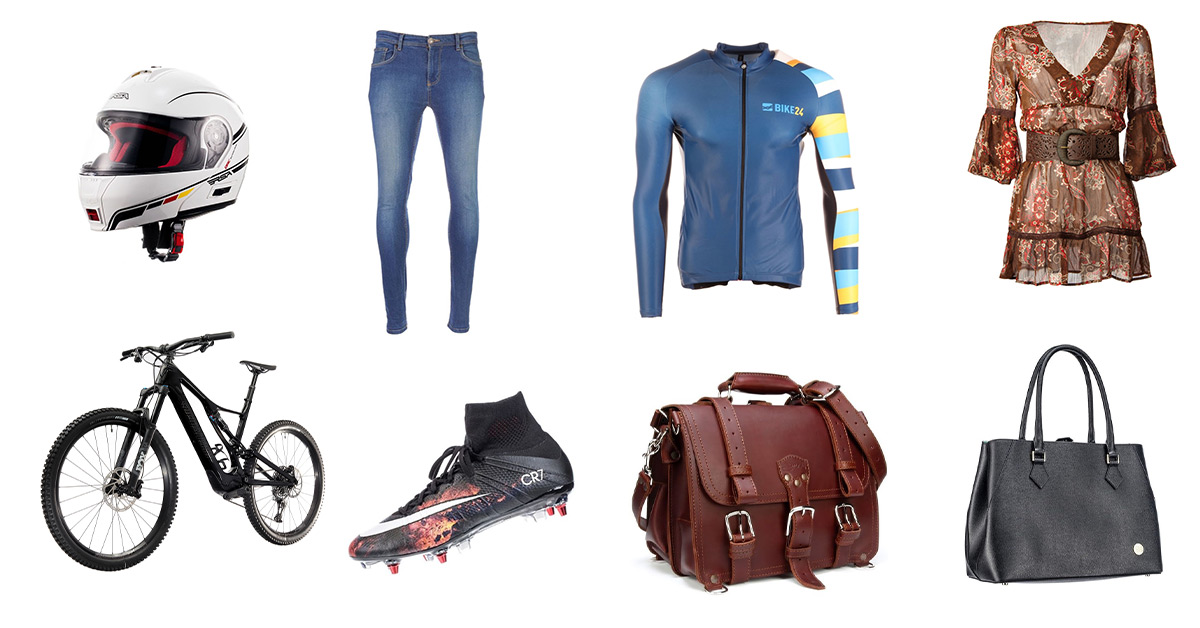
Standardized production for small to large teams
The Cube Compact and its software aim to standardize and streamline higher volume production workflows. They help professionals work more quickly and more efficiently while in sync with several other people, or larger production teams.
For example, the technology connects all stages of the production workflow: product prep, photography, post-processing, and file management. For this, the built-in, industrial operating system features real-time, cloud-based workflow software to connect various workers in their roles. This includes production managers, machine operators, stylists, or any internal as well as external talent like outsourced QA or retouching.
Moreover, the industrial operating system makes it easy to connect and synchronize multiple PhotoRobot modules at once. It connects the Cube to 360 turntables like the Case 850, and is compatible with many PhotoRobot devices. Think: multiple workstations, using the Cube standalone or in combination with turntables and robotic camera arm systems. It might even be 10, 20, or 60 Cube workstations operating in the same space.
The pre-programmable controls, API integration, and cloud-based asset management makes it possible to align all members of production.
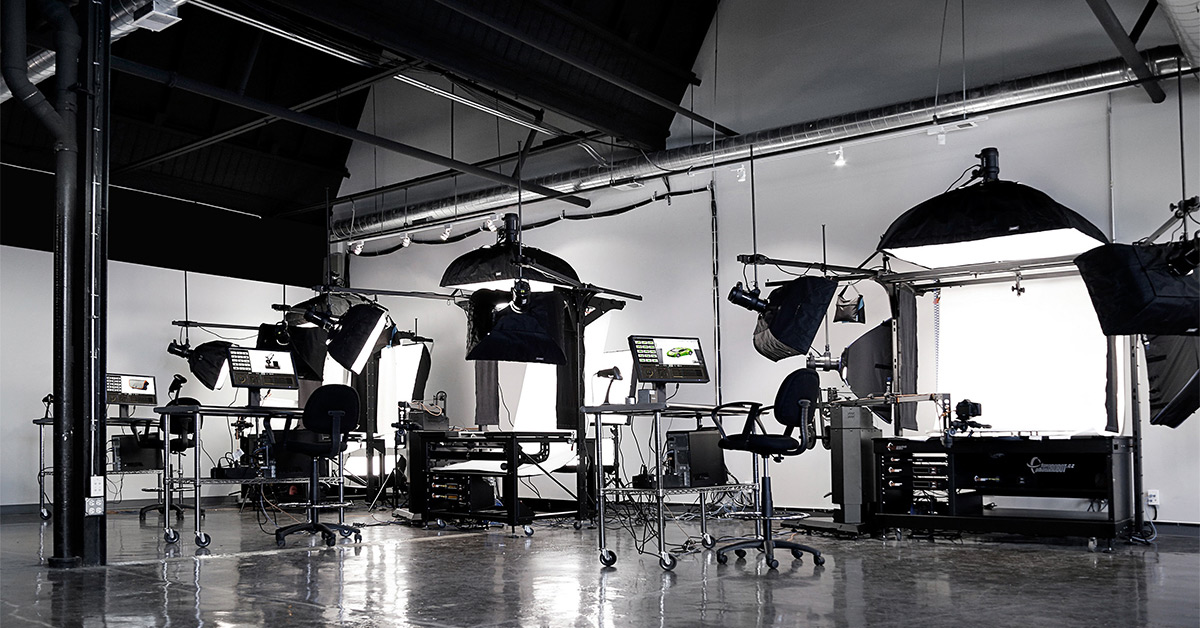
Exponentially faster with each additional machine
Like all PhotoRobot systems, the Cube Compact aims to maximize long-term production and throughput for even the largest scale operations. Imagine for example a manufacturer or distributor working in an industrial warehouse with 60+ Cube workstations at once.
In this scenario:
- 60 + robotic workstations fit into a space of approximately 25,000 square meters.
- The space can be a natural warehouse environment, without any climate controls.
- Each workstation offers a production time of roughly 1 minute per product.
- That’s nearly 500 items per machine per 8-hour shift.
But what about all 60+ machines in operation for two 8-hour shifts per day?
- 500 items x 60 machines x 2 shifts = upwards of 60,000 items per day.
- That’s with full sets of automatically post-processed outputs: galleries, packshots, and 360s.
- Outputs are often web-ready, with minimal to zero need for retouching.
- It is also possible to instantly and automatically publish images online.
Obviously, production doesn’t always go 100% to plan, but we know firsthand that achieving throughput like this is possible. In fact, there is a client in PhotoRobot’s portfolio that reaches production levels extremely close to the above scenario. Using 60 Cube robots, this business photographs on average 40,000 fashion items daily, in only two 8-hour shifts.
This is even accounting for delays in production and various obstacles. Thus, we know this setup can reach on average 40k items per day with ease. Now, imagine adding a second factory with 80+ robots to this equation. And remember, all robots and systems are fully integrated via the software and API connection. They also receive remote software updates simultaneously, and are easily cleanable in between shifts.
Starting to see the possibilities here?
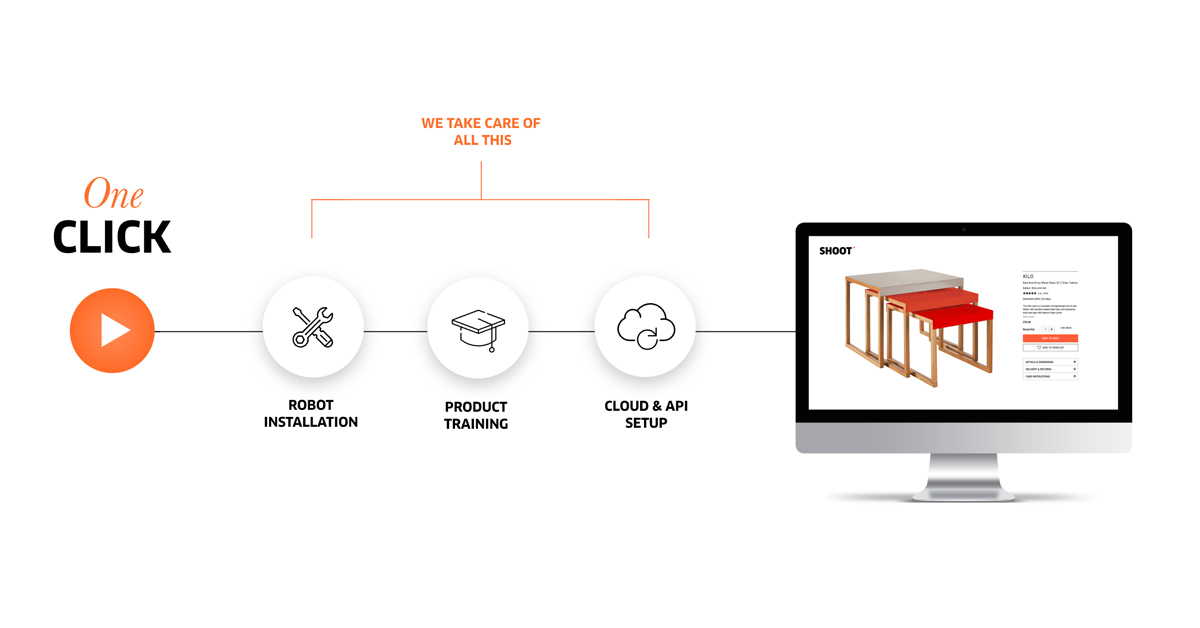
Demos tailor-made to the business’ needs
Curious to see how PhotoRobot might be able to integrate into your business’ photography? PhotoRobot demonstrations consist of photographing your product line or similar products with our solution. We first consult on your needs, and then build a tailor-made module consisting of one or multiple robots.
On top of this, we measure exactly how long it takes to photograph each item, and create detailed documentation. This includes integration manuals, as well as recommended cameras, computers, and equipment. We then install your custom studio configuration in the PhotoRobot showroom so you can see it in action.
In this way, there are no unexpected surprises when clients begin their own production. They can demo everything in-person, or see the live test via video conference.
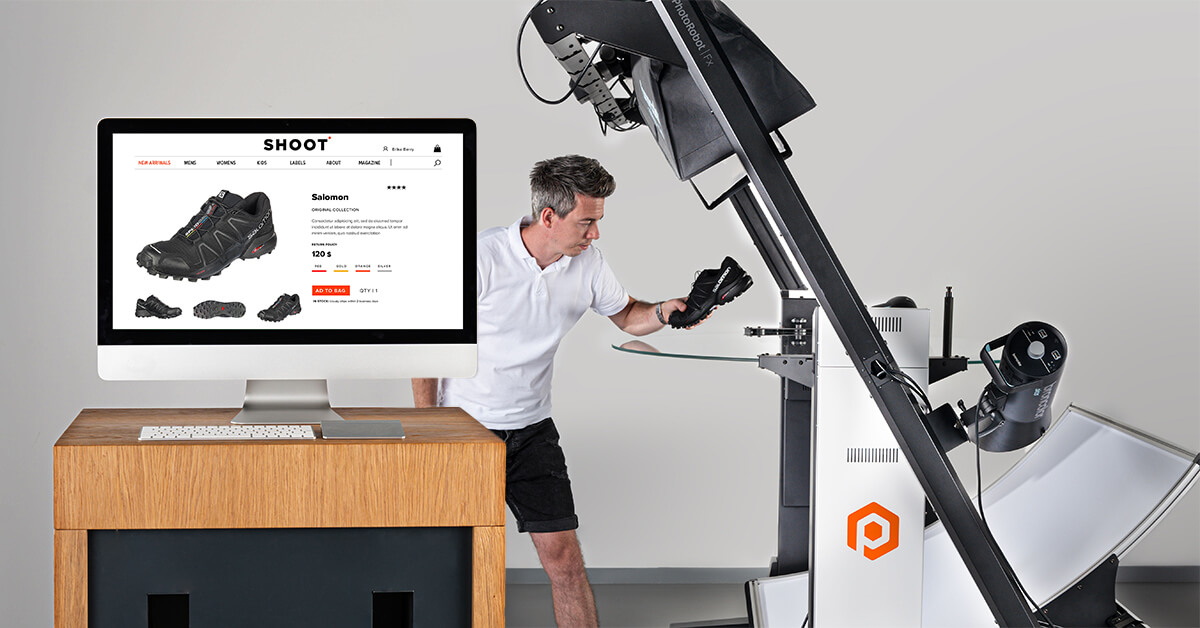
Smooth onboarding and integration
After agreeing on a configuration, PhotoRobot transfers the technology to the client. This involves installation of all equipment on-site, user training, and help starting production. Usually, this takes only a few days to a week for the entire process. Then, with clearly defined benchmarks from the demo, the business can begin operations. PhotoRobot experts are also at this point on-hand to integrate any new ideas clients have into their studio workflows.
Do you have a business idea you’d like to see if PhotoRobot can manage? Just reach out and let us know the unique problem you are trying to solve. Our technicians are ready and available to see you from demonstration to production.